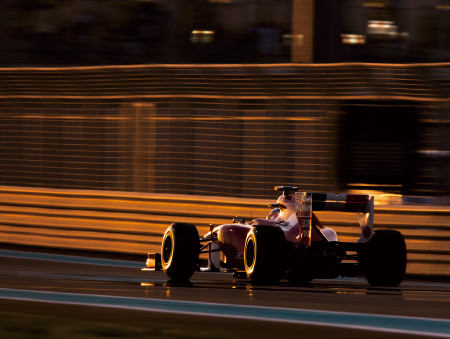
Thriving on our motorsport DNA.
Originating from BBS Automotive Technology AG in Germany, our BBS brand has been honed through a deep involvement in motorsports. Currently, in the course of supplying wheels for a number of motorsports, we conduct tests during development with the collaboration of racing teams. And, besides the actual running data, we also feed back to our product development the detailed information on the running sensation that we pick up from our interactions with racing drivers. This is something that cannot be obtained from analysis software. We want drivers in the general public to also be able to feel a running sensation that has been hardened in the extremes of the racing world. And, both our racing wheels and aftermarket road wheels are crafted with that frame of mind, in the same factory, by the hands of the same craftsmen.
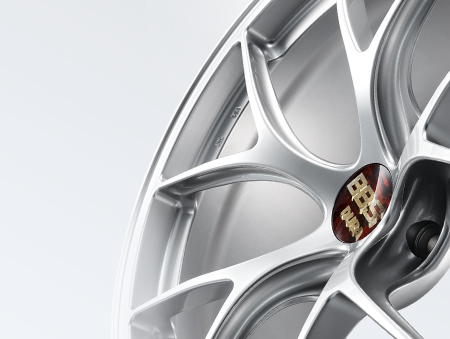
The ultimate design for performance, driving or racing.
Motorsports are conducted under strict regulations, particularly those related to materials, size, and weight, down to the fabrication of each wheel, and all of these elements must serve to enhance the running performance and reliability. Our unique cross-spoke design, which is synonymous with the BBS brand and is consistent across all of the products in our line-up, features back-milled spokes and is a form developed through our thorough examination or study of mechanics. This design is the ultimate in functional beauty, exhibiting high performance in all types of situations, and has been made a reality by the forging technology we have honed over the years.
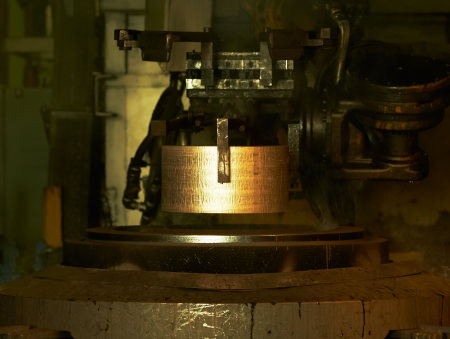
Aspiring to the highest level: a forging ratio of 4 or more.
The BBS commitment to forging lies in forging cast billets with a forging ratio kept to 4 or more. By taking the time and effort when compressing, the cast structure is formed into a forged structure that enables the beautiful grain flows to form (metal flow lines) down to the smallest detail. The philosophy of craftsmanship at BBS is, so to speak, lavishly pouring the very best technology currently imaginable into each and every wheel.
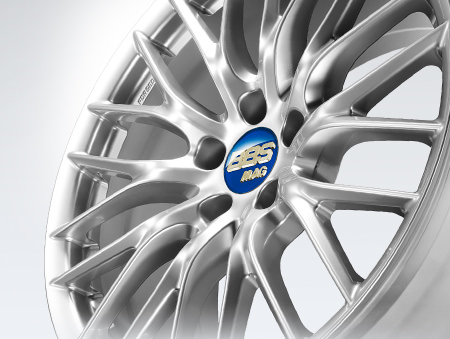
Our insatiable challenge to use new materials.
In materials as well, BBS continues to tackle challenges ahead of the rest of the world. Aiming at creating a lightweight wheel, we developed the world's first forged extra super duralumin wheel in 2011. Since extra super duralumin features impressive strength compared to conventional aluminum, the most difficult part of using it as a material was optimizing the stiffness of the wheel. While amassing data by repeating actual running tests and verifying the comfort of the ride and shaking of the steering wheel many times, we were able to achieve an ideal balance. In addition, in order to overcome the weakness to corrosion of mass-produced forged magnesium wheels, we worked at developing a special surface treatment that led to a coating performance equivalent to that of aluminum, and that enabled us to achieve mass production of forged magnesium wheels in 2015.
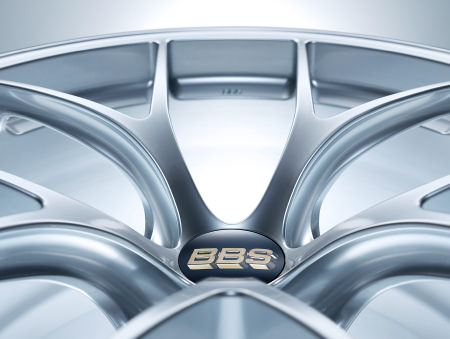
Our pursuit of toughness: light, strong and supple.
In the world of motorsports, where the action unfolds at extreme limits, survival only by having high marks for being lightweight and rigid is not possible. The most important characteristic that BBS wants its wheels to have is the power to hold on. Or put another way: toughness. Toughness: where strength comes from the wheel being forged to be strong, and where resilience enables the wheel to have a supple flex. When the wheel is suddenly impacted, BBS forging technology enables the impact to be controlled by flexing the wheel to prevent it from breaking.
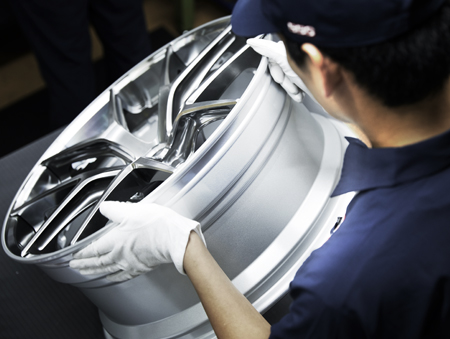
Carefully finished with a craftsman's eyes and hands.
Surface defects such as wrinkles during the forging part of the manufacturing process and tool marks caused by milling removal of material infrequently occur. Surface imperfections that tend to be overlooked in the material state are exposed after inspections at many stages and are visually caught and smoothened manually by our craftsmen. In addition, the backs of the wheel spokes are given a very smooth finish. The reason for this is that, if an edge even partially remains, a crack can form there allowing corrosion to progress. The overwhelmingly high quality of BBS products is supported by the careful attention of our expert craftsmen who take the time on fine points that may not even be seen by anyone.
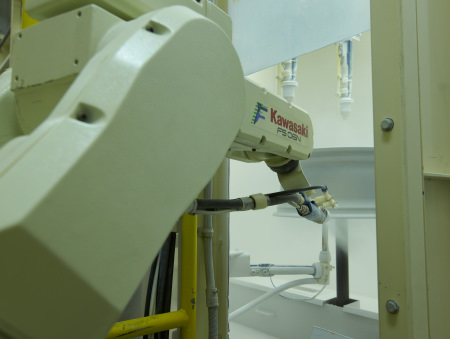
Each of our craftsmen tackles their challenges as a BBS fan.
We gather all of our customers' opinions and requests, and respond sincerely to each and every one to reflect them in our products. This is the basis of our craftsmanship at BBS. And beyond just taking the customer's point of view, our craftsmen try to look at BBS as consumers, as though they were customers themselves. We believe that there is always room for improvement, and that is why we are able to improve. BBS wheels are hardened by the passion of our fans, and we will continue to further enhance this superior position that we exist in.
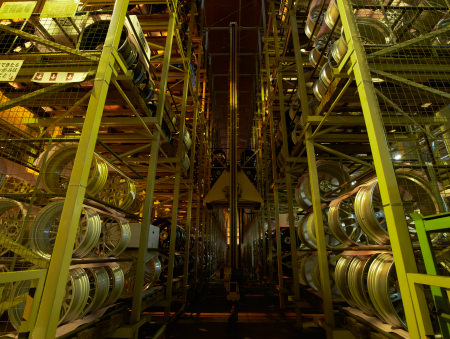
Our own quality control learned from automobile manufacturers worldwide.
BBS continues to supply wheels as OEM equipment to famous automobile manufacturers throughout the world. In addition to complying with the different quality criteria of each manufacturer, to achieve absolute quality BBS also applies its own standards for aftermarket road wheels that are based on the most rigorous of inspections. We control our quality at a high level.